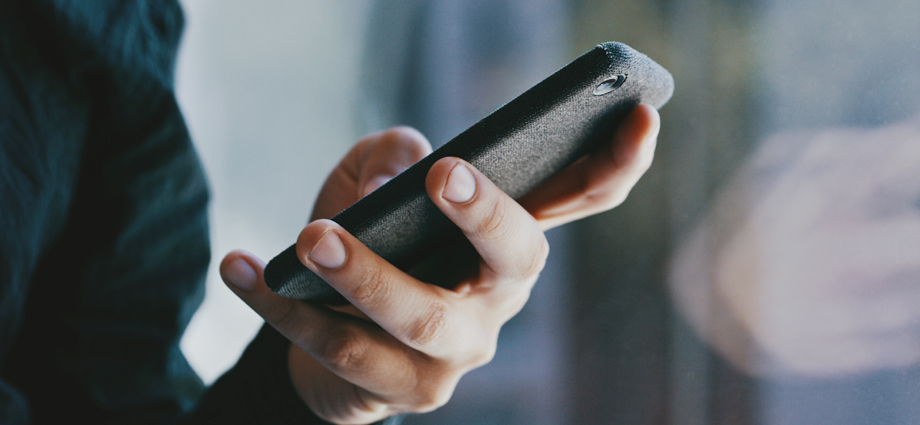
The year was 1987. Star Trek: The Next Generation Fans were mesmerized (and, perhaps, rather envious) when Captain Jean-Luc Picard told a simple box machine to deliver on his command: “Tea, Earl Grey, hot.”
Now, of course, not only is that kind of technology possible, it’s also quite common, thanks to connected smart devices, cloud data, and automated notifications.
For many, it’s both convenient and helpful to use connected devices to remote-start a cold car or get timely reminders to descale the coffee maker.
With such technology literally at our fingertips, have you ever wondered why the same can’t be said within your HVACR systems?
Why can’t our $500K machine tell us when it needs to be calibrated or maintained?
Why, indeed! Perhaps the better question is, Why doesn’t our BAS equipment supplier offer this?
The truth is, there is technology available right now that enables exactly that. And, frankly, it’s far more game-changing than a cup of hot Earl Grey.
Remote Connectivity and Real-Time Notifications
I talked about this topic during my presentation at last week’s AHR Expo in Las Vegas. Everyone else was talking about the value of connectivity and the cloud within the HVACR industry, too.
But for those of you who may have missed out, here’s a recap of the most common problems facing HVACR, along with the fix for helping prevent failure of high-value assets.
Problem: The biggest contributor to chiller failure is infrequent or improper maintenance.
The Connectivity Fix:
- Intelligent, predictive maintenance
- Automated checks to ensure optimal working conditions
Problem: Overheating and other factors like voltage unbalance and poor ventilation contribute to electric motor failure.
The Connectivity Fix:
- 24/7/365 remote machine monitoring
- Remote configuration and programming
Problem: An overlooked or neglected boiler increases energy consumption, reduces performance, and poses a threat to safety and well-being.
The Connectivity Fix:
- Pre-emptive notifications
- Asset optimization
FieldServer and You
Of course, these are just a few examples of what can happen to your systems and how technology plays a role in overcoming such challenges.
The point is, when you don’t know how your assets are performing and you don’t have a reliable method for ensuring proper and regular maintenance, your operations are at risk of catastrophic failure.
There is a better, more connected way: the MSA FieldServer suite of automation gateway products and FieldVEU, an MSA Grid cloud solution.
How It Works
Imagine your high-value asset sends you a text, notifying you that there’s a problem. Before you go scrambling to figure out where and what, the text already has you covered.
- It details what the issue is.
- It provides a URL to machine web interface.
- It enables you to use your mobile phone to look at the interface.
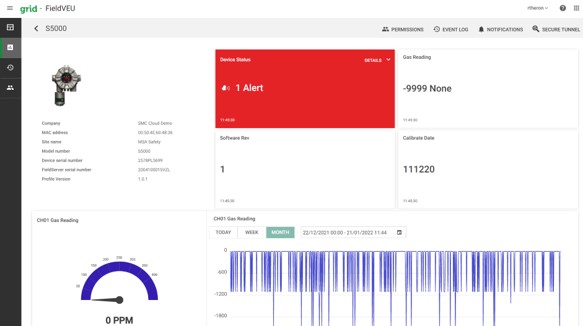
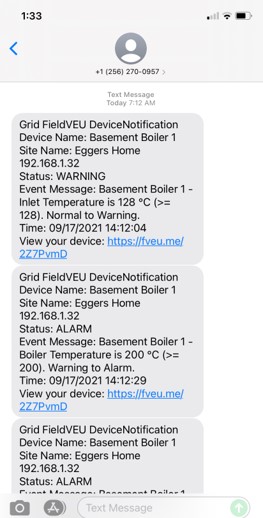
Bottom-line, it sends the right information to the right person at the right time, providing full visibility and actionable insights on your assets.
If you’re ready to learn more about how applying this technology to your organization can help you “get the message,” please email us.