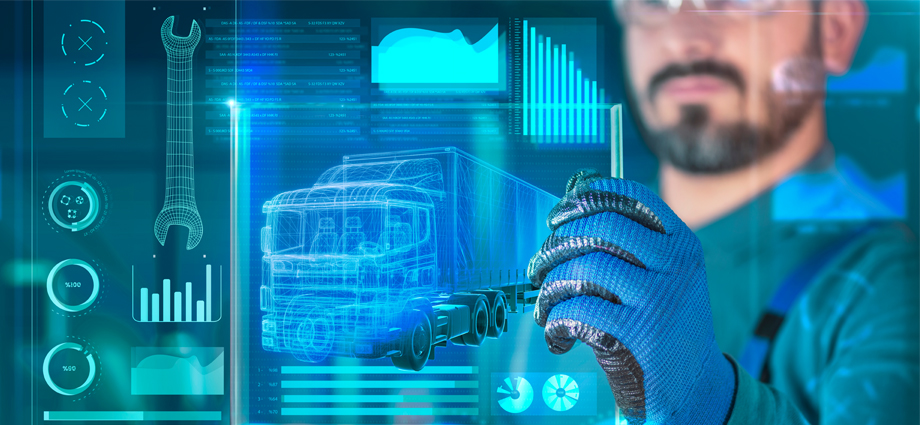
Somewhere between Evansville, Indiana, Kapolei, Hawaii, and Hazira, India is a compressed air system alarm, voltage disturbance, or some other anomaly that requires swift and specialized attention.
Enter Case Controls®.
With installations across North America and around the world, troubleshooting, monitoring, and supporting issues is all in a day’s work for this Evansville-based firm that designs, builds, and services world-class products for controlling industrial air compressors and compressed air systems on Allen-Bradley CompactLogix™ and ControlLogix® PLCs and PanelView™ Plus HMIs.
Case supplies and services some of the world’s most well-known – and most depended-upon – industrial organizations. In fact, without Case’s support, some of these compressed air operations could be severely interrupted or even shut down, negatively impacting the production and distribution of essential food, healthcare, paper goods, and other much-needed supplies.
THE CHALLENGE
Though they were already known for providing outstanding service, Case knew it could amplify its support offerings even more – and save customers time, money, and downtime hassle – if they could figure out how to expand their compressor data monitoring capabilities.
For the past two years they’d already been relying on MSA FieldServer™ for IoT solutions and multi-protocol gateways. So, Case again turned to FieldServer and presented this challenge:
THE SOLUTION
FieldServer acted as swiftly as the implementation of its solution. Within just a couple of weeks, it delivered a robust platform that allows Case to offer customers speedy remote troubleshooting, diagnostics, and remote connectivity.
AirView™ Cloud, the data visualization solution on the compressor controller, is a versatile platform that has exponentially expanded Case’s compressor data monitoring abilities – to the delight of its team and its customers.
With AirView Cloud, Case can now remotely connect to any of their partnering customer locations anywhere in the world using a secure connection. AirView Cloud lets them acknowledge an issue, and either resolve it in mere minutes or determine whether Case needs to schedule a site visit.
Plus, with the OpenVPN solution from FieldServer, Case engineers can remotely access the Allen-Bradley hardware on each compressor and using the Allen-Bradley development software, reconfigure or troubleshoot the controllers. The virtual tunnel via the FieldServer Cloud also allows for Compressor local HMI web based screens to be viewed remotely.
“Thanks to FieldServer, the answer to our problem turned out to be surprisingly swift and simple… They delivered an out-of-the-box solution with all the bells and whistles, and implemented it in less than 14 days. We now have the ability to respond almost immediately and resolve compressed air system issues to improve system efficiency and increase overall system reliability. We appreciate both the functionality of the FieldServer solution and the price point. In fact, we’re so pleased, we’re now thinking of placing FieldServer on each control system we sell and service.”