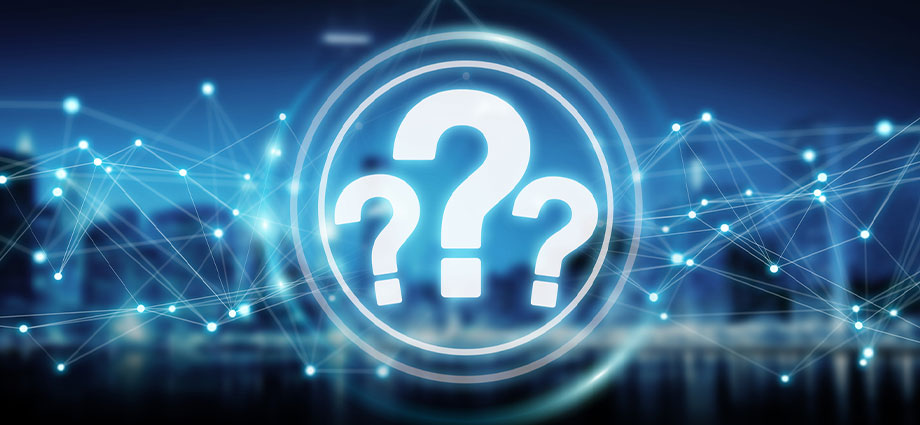
Asking the right questions is a key component of good decision making. It gives you the opportunity to learn details, exchange ideas, and challenge conventional thinking. Most importantly, it leads to better conclusions.
In fact, according to an article in the Harvard Business Review, only 15 to 25% of adult professionals polled said they regularly asked questions. This is compared to almost 80% of children who – as most of us know – ask a ton of questions.
The reasons for this are many and varied, however, the article inferred that a big reason was the workplace decision making has made a dramatic shift from “get it done as soon as you can” to “get it done yesterday.”
You Don’t Know What You Don’t Know
But not taking the time to ask the right questions just so you can “get it done” can be costly in terms of both time and money. Perhaps 16th century philosophy Francis Bacon best summed up the power of asking questions when he said: “A prudent question is one-half of wisdom.”
Which is why we wanted to do a virtual Q&A on a topic we get asked about all the time: Cloud-based Industrial Internet of Things (IIot) solutions.
Answers to Questions about Cloud-Based IIoT Solutions
If you’re on the connectivity journey or looking to leverage the Cloud for your automation systems, keep reading to get answers to some essential questions.
Q: Everyone’s talking about connecting field devices to the Cloud, but it seems like a lot of work. Is it worth it?
The short answer is: Yes. The long answer is that everyone is talking about Cloud-based automation solutions because of what the Cloud can do – which is promote secure, intelligent, efficient automation.
As for being a lot of work, that depends on how you go about implementing your Cloud solution. Finding the right partner is essential. At MSA FieldServer, we make it easy to modernize building automation, industrial automation, energy management, and life safety systems through Cloud-enabled equipment. Contact us to learn more or start by checking out our series on Third-Party Integration here.
Q: How does Cloud technology work in the industrial automation world?
Very well, thank you. All joking aside, here’s a visual that can help you understand how it works:
And here are some of the many benefits of Cloud technology for industrial automation:
- Autonomous operation and programmed automation
- Remote configuration, diagnostics, and troubleshooting
- Multi-user, multi-device accessibility
- Location independent, real-time monitoring
- Scalability
- Systems, resources, and operational optimization
- Unlimited virtual storage
- Reliable, persistent situational awareness
- Streamlined reporting and compliance
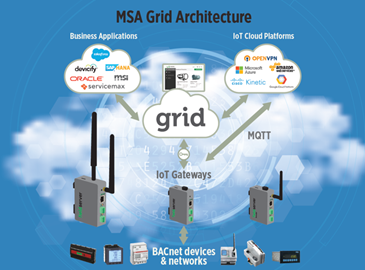
Q: We want to have a Cloud strategy but where do we start?
Congratulations! Given its many benefits, it’s understandable that you’re anxious to get going and take the leap into intelligent automation. We suggest, however, that you take your time and partner with someone who can guide you through the transition. The starting step, then, is to find a connectivity partner and learn from them.
Next, look at your systems and compare them with your overarching objectives for implementing a Cloud strategy. This will help you determine what to prioritize first. Then look for the proverbial low-hanging fruit. Determine which area of your operation offers the greatest opportunity for a return. Where can you achieve the most meaningful outcomes while using the least number of resources. Finally, remember that technology changes quickly so adjust your expectations accordingly. Cloud computing for industrial automation is not a “one-and-done” undertaking. So, move forward deliberately, ask questions, and learn as much as you can before you make any decisions.
Q: Is connecting to the Cloud going to put us at risk for cyberattacks?
Smart question. When it comes to Cloud connectivity, cybersecurity is an extremely important consideration. Our goal is to help our customers eliminate exposure to their entire organization. We’ve developed several products to help us do that, like the MSA FieldServer Dual Ethernet Port Device. Among its many capabilities is that it allows for secure LAN or WAN connectivity while blocking VPN and proxy tunnel.
As a rule, remember that connecting to the Cloud brings with it some inherent risks. Be sure to ask your solutions provider what they’re doing to mitigate these risks. Then make sure their answers include such measures as:
- Industry-standard password policies
- User verification requirements
- Encryption to restrict access
- Annual penetration and vulnerability testing
- Comprehensive incident response plan
Q: We have a lot of disparate devices from different manufacturers along with legacy components that are too expensive to replace. Can we keep them and still connect to the Cloud?
Absolutely! While start-up organizations have the advantage of investing in the latest and greatest technology (for now, anyway), established OEMs and other companies shouldn’t have to invest in new devices or costly IT infrastructure to leverage the Cloud.
As an example, the average industrial plant has a mix of new and legacy devices that can be swiftly, seamlessly, and more affordably integrated, thanks to MSA FieldServer gateway products, including Modbus, Ethernet/IP, GE-EDG, and a host of other state-of-the-art protocols. Learn more about no-hassle legacy integration here.
Q: Are Cloud-based applications and platforms expensive?
They don’t have to be. We’ve developed connected, Cloud-based solutions that don’t require significant upfront investments or expensive add-ons. Affordable alternatives do exist. For example, we offer one-box solutions in the form of our FieldServer portfolio of products. In fact, we believe that the right Cloud-based applications and platforms will save you money.
Q: When our company data is in the Cloud, can others using the same Cloud see our data?
Not with the MSA Grid. That’s because it is a tenant-based system, which means that your data is separate from anyone else’s. MSA Grid customers cannot see another customer’s data – and neither can MSA, unless the customer wants us to see it so we can offer technical support.
Q: Can I move my Cloud data to other Cloud applications?
With the MSA Grid, the answer is yes. The Grid has two APIs or application program interfaces, that define how applications or computers talk with one another. The Grid allows you to move data to third-party Cloud, notably a RESTful API and Webhooks. A RESTful API is what lets you retrieve data from one place and display it somewhere else. A Webhook works similarly, only it uses automated messages.
Q: Will moving to a Cloud-based solution for remote monitoring, configuration, and data capture/analysis slow us down?
On the contrary. With proper implementation of a highly secure, robust Cloud solution, you can expect to streamline operations, improve safety, save money, support your customers in the best, most time-efficient manner, and a whole lot more.
Q: How soon can I have a go-to-market solution up and running?
Very quickly with MSA. That’s because at MSA, once we fully understand your objectives, we can get you up and running with a sample within two weeks, and help you determine the right Cloud solution to benefit you and your customers.
Want to learn more? Talk with an MSA Sales rep today.