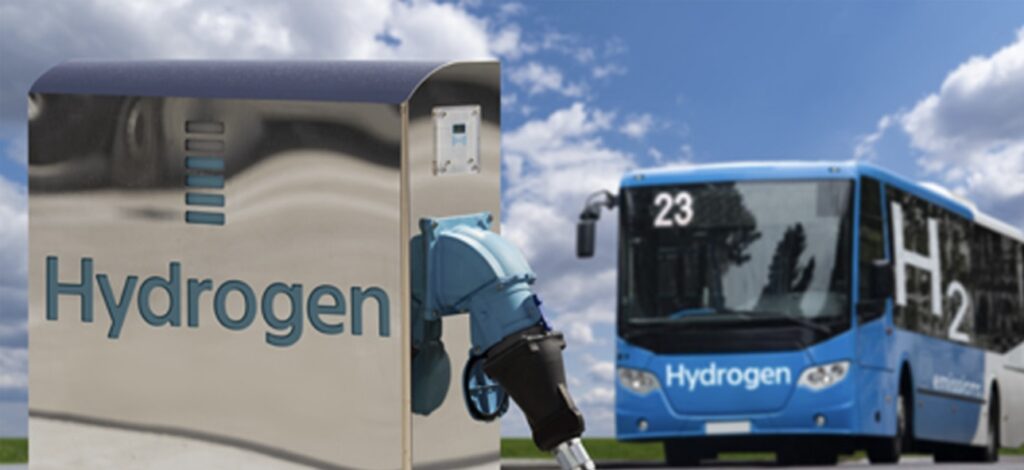
The world is in a race to drastically cut CO2 emissions in support of climate change goals, with many countries targeting net-zero emissions by 2050. This an ambitious undertaking, of course, but one that’s not without its share of safety concerns.
- What are the potential hazards of hydrogen production?
- What safety challenges need to be addressed?
- How can IoT automation help organizations incorporate green hydrogen into their energy strategies more safely?
As large-scale hydrogen production continues to ramp up, now is the time to take a closer look at the potential safety challenges of this clean, renewable energy source. More importantly, now is the time to take a closer look at what can be done now to help ensure hydrogen safety.
The potential safety hazards of hydrogen production
Although we’ve written about safety measures and detection technologies for hydrogen before, it never hurts to review the properties of hydrogen gas that make it a desirable fossil fuel alternative as well as a potential hazard:
- Hydrogen is environmentally friendly and sustainable.
- Hydrogen is colorless, odorless, and tasteless, making it undetectable by human senses.
- Hydrogen has a propensity to leak.
- Hydrogen has an invisible, high-temperature flame with low thermal radiation.
- Hydrogen is fast detonating and more explosive than natural gas.
According to the U.S. Department of Energy, Office of Energy Efficiency & Renewable Energy’s Safe Use of Hydrogen, all fuels (including hydrogen) have safety concerns. On one hand, hydrogen is safer to handle and use than some fossil fuels. On the other, despite its non-toxic nature and propensity to dissipate rapidly when released, hydrogen can ignite more easily than gasoline or natural gas.
So, when it comes to designing hydrogen system infrastructure, appropriate ventilation and leak detection are key to ensuring safe hydrogen production, use, and storage.
Safety innovation in the transition to hydrogen fuel
That’s exactly what the Champaign-Urbana Mass Transit District (MTD) did, starting in 2018, when it became the nation’s first transit agency to order a fleet of 60-foot articulated hydrogen fuel cell buses. This monumental shift from fossil fuel-powered vehicles to green transportation necessitated an upgrade to MTD’s infrastructure and technologies to accommodate this new fleet as well as expand the MTD terminal.
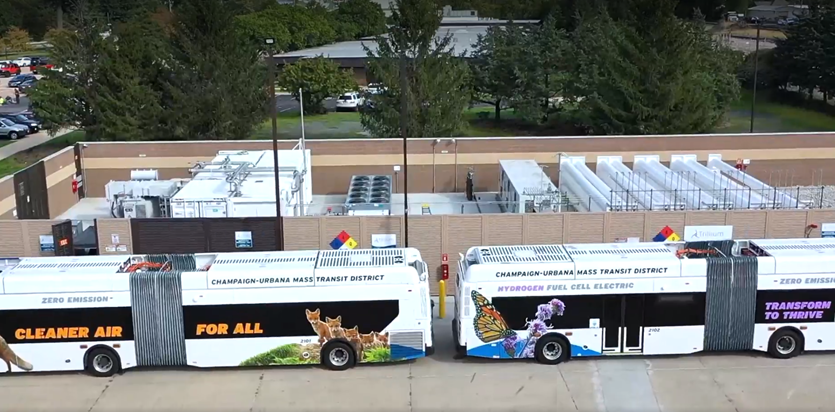
Here’s how MSA and FieldServer helped this future-forward mass transit organization ensure the safety of both their employees and high-value assets in an environment that’s also home to an on-site hydrogen production station.
How do IoT automation solutions help keep hydrogen production safe?
“Our zero-emission fleet technology is an advancement in climate resiliency,” says Kirk Kirkland, Facilities Director for MTD, “It literally put us on the cutting-edge of public transportation powered by clean fuel. To get to this point, however, we had four projects in the works all at the same time: building the buses and bringing them on-site, a temporary fueling station, installing a two-megawatt solar array field of nearly 5,500 panels, and constructing a hydrogen station. We needed a reliable system that not only could detect hydrogen, nitrogen dioxide, and carbon monoxide gasses, but also immediately notify us if there was a leak or potential hazard.”
“We needed a reliable system that not only could detect hydrogen, nitrogen dioxide, and carbon monoxide gasses, but also immediately notify us if there was a leak or potential hazard.”
Kirk Kirkland, Facilities Director MTD
What MTD needed was an independent life safety and automation solution that provides remote equipment monitoring, control, and alarming.
Hydrogen monitoring, alarms, and fire safety
Because hydrogen is a highly flammable, colorless, odorless gas, early detection and notification of gas leaks and flame are critical to ensuring safety.
Since MTD was the first transit agency in the country to adopt a hydrogen fleet fueled entirely from their own 100% renewable source, there was, of course, a steep learning curve for just about everything—including safety.
MTD determined that the best solution for their new hydrogen station and production plant was the SMC Sentry fixed gas detection system, featuring:
- Advanced sensing algorithms
- Protocols
- Web technologies
- Cloud connectivity
The system, paired with the FieldServer ProtoNode, enables MTD to connect the Sentry IT system to the FieldServer Manager and receive real-time text and email notifications to alert key personnel to the potential presence of hazardous or combustible gases.
“The bus garage is not the best place to see or hear alarms,” explains Kirkland. “A hydrogen system with built-in alarms, horns, and lights that’s like a fire alarm is good, but for nitrogen dioxide and carbon monoxide, we needed something better than just a light on a panel. We needed the Sentry IT with ProtoNode.”
Not only has this MSA connected solution empowered MTD with monitoring and communication capabilities from a remote location for fire safety, it’s also compliant with local fire department regulations for times when no personnel is on site to physically monitor the system.
Hydrogen safety solutions: monitoring hydrogen, nitrogen dioxide, and carbon monoxide
MSA and FieldServer’s combined system provides MTD with a nimble and scalable solution that enhances the way notifications are handled. This is especially important since MTD has 100+ IIoT automation devices generating hundreds of combined notifications.
“Obviously, we’re most concerned with hydrogen,” says Kirkland. “In fact, some of our team members only want to see hydrogen alarms. This system is great because it lets them choose the parameters they want. But we also have to monitor nitrogen dioxide and carbon monoxide. This system gives us confidence that we’ll have the notifications we need should there be a higher concentration of any gas or if any of the gases are present for too long.”
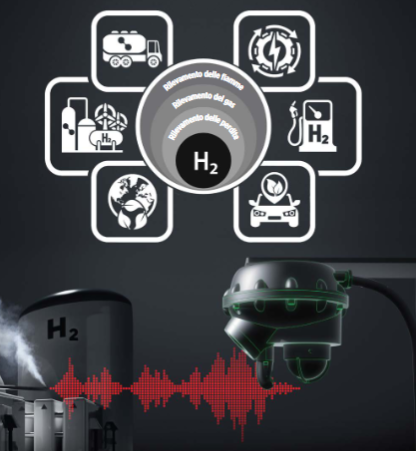
Working Safely with Hydrogen
Download our white paper to learn about solutions for workplace safety risks and challenges posed when producing, handling, transporting, and storing hydrogen.
DOWNLOAD WHITEPAPERHydrogen fueling station safety
The addition of the FieldServer ProtoNode to the Sentry IT gas detection system is essential to delivering a complete safety solution. ProtoNode is a high-performing, low-cost IIoT gateway that enables both SMS text and email notification for trouble or alarm conditions.
“Things are working very well,” says Kirkland of the MSA and FieldServer solution. “We’ve set up the types of events we want to monitor, and we’ve configured the high-low settings we want for hydrogen. We’re absolutely confident that it will do everything we want and need it to do to keep our first-of-its-kind zero emission fleet technology and our staff safe.”
The future of hydrogen safety
When it comes to safety, MSA’s Sentry IT and FieldServer ProtoNode are enhancing the safety and efficiency of trailblazers like MTD who are leading the transition from diesel to low-emission vehicles. Whether its leak detection to reduce the risk of hydrogen fire or explosion or proactive monitoring to mitigate exposure to toxic gases, the MSA-FieldServer one-bundle solution exemplifies the best in IoT-based automation systems within the renewable energy sector.
To learn more about MSA’s connectivity solutions that enhance safety and efficiency, contact an MSA Sales rep today.
More safety resources