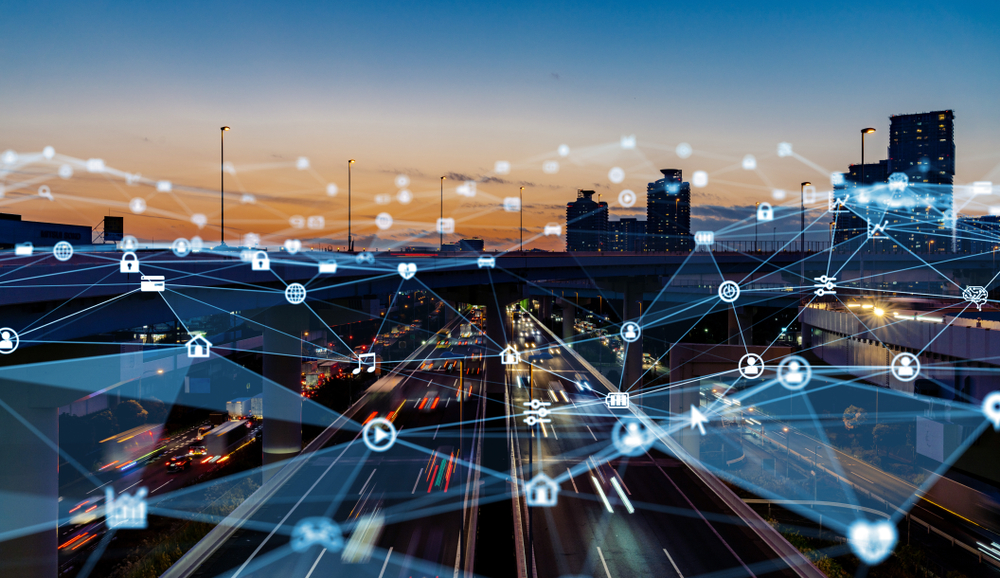
If there’s one universal constant with commercial and industrial devices, it’s that downtime costs money. If the devices that operate a manufacturing facility, or a commercial building go down, there’s a cost in getting them diagnosed and repaired. But there’s the other cost, as well – the cost of decreased productivity.
This is easy to visualize in a manufacturing environment. Any slowdowns on the production line caused by failing or malfunctioning equipment obviously impact production and decrease profits. But this is equally true with commercial buildings like office buildings and corporate campuses.
If the elevator fails in a multistory building, there’s a chance that people will get to their desks later – or not at all if they have special needs. If the boiler fails or the air conditioning fails in the middle of winter or summer, there’s a chance that the working conditions could become unsafe and employees could be sent home. In each of these instances, productivity and revenue are ultimately lost.
To combat this, equipment owners are looking to identify failing devices sooner and work to proactively service and repair them. While this doesn’t eliminate the cost of having a repair technician service the equipment, it does save on the lost productivity that results from that device failing outright and unexpectedly. And that productivity loss is something that could extend for multiple days should a device fail since the technician most likely would have to come out multiple times – once to diagnose the problem and again with the appropriate and necessary parts to repair the device.
EQUIPMENT FAILURES ARE A SIGNIFICANT COST TO DEVICE OWNERS. PROACTIVE MAINTENANCE CAN HELP KEEP DEVICE ISSUES FROM ESCALATING INTO DEVICE FAILURES, BUT ONLY IF THE DEVICE OWNER KNOWS THERE’S A PROBLEM.
To make proactive equipment maintenance and servicing possible, the equipment owners need device data. Without access to device data, there would be no way to know that a motor is starting to draw extra power – a sure sign of motor failure – or another warning sign is occurring. This requirement is being met by equipment manufacturers that are increasingly network-enabling and cloud-enabling their devices. This makes device data available to the building owners from any location with an active Internet connection.
But is that really enough for equipment owners to make proactive maintenance decisions?
Pushing logic to the edge
The average equipment owner probably doesn’t know that decreased airflow could be an indication that filters need to be changed. They may not know that extra energy being used by the motor is a telltale sign of motor failure. They just know that their devices are essential for the operation of their business and that they don’t want them to fail.
Just getting a stream of equipment or device data isn’t enough for the average equipment owner to make any kind of predictive maintenance decision. Worse, pushing all of that device data into the cloud could come with cost considerations – cloud costs increase when data sets grow.
The answer to this problem is to push some of that data analysis and filtering out into the field, where the device lives. This is a concept that is often referred to as “edge computing.”
In an edge computing environment, some of the compute power and logic is decentralized and moved to where it’s most needed – out where the data sets are being generated. This accomplishes a number of things, it helps reduce the sheer amount of data that needs to be transmitted into and stored in the cloud, helping to reduce cloud costs. It also means that the data that’s being pushed is pre-filtered in such a way that the end-user isn’t just receiving data sets in need of analysis, but actionable insights.
How does this edge computing concept apply to the proactive maintenance situation that I described previously? Pretty exceptionally.
Edge computing doesn’t have to mean that there’s a powerful compute resource at the edge. It could be a simple and stripped-down device that’s incredibly cost-effective but still capable of solving problems, filtering data and translating data on-site.
Take, for example, an IIoT cloud gateway.
Cloud gateways can be used to simply push data up into the cloud and into a BMS system. But they can also be programmed to apply logic and filters to data. They can be used to filter data for red flags and actionable insights. They can also be programmed to send out alerts when device data meets or exceeds certain thresholds.
What could that look like? To use an earlier example, parameters could be set for acceptable motor energy consumption. Should consumption exceed those parameters, an alert could be issued that warns the equipment owner that the motor is potentially in need of service. From there, the device could even be remotely throttled down or powered off to keep it from failing completely.
Equipment failures are a significant cost to device owners. Proactive maintenance can help keep device issues from escalating into device failures, but only if the device owner knows there’s a problem. But just getting the device data isn’t enough. By implementing edge computing initiatives – even if accomplished with simple cloud gateways – device owners can get more than just data. They can get actionable insights and warnings to help ensure that no device issue goes unnoticed.
For additional information on how edge computing and cloud gateways can enable proactive maintenance in commercial and industrial devices, contact us today!