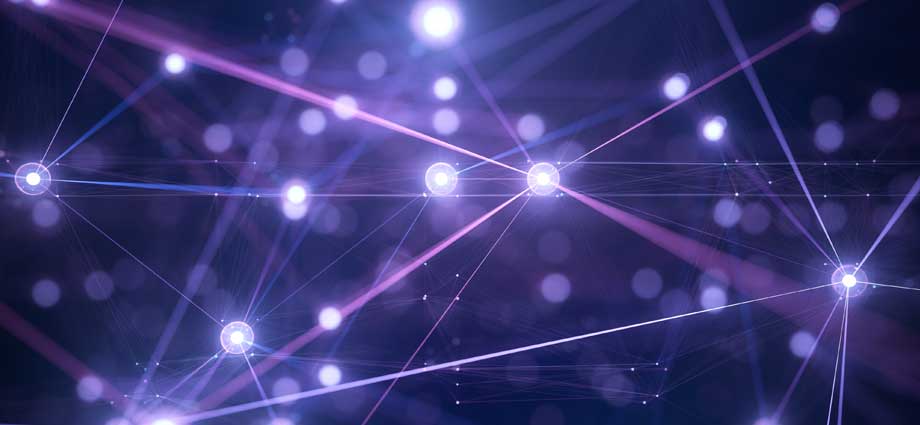
The world of safety is in the midst of a revolution – the IIoT (Industrial Internet of Things) revolution where technology can enable a better, safer, more productive work environment.
Nowhere is this as important as it is in industrial settings; industrial settings where combustible gas and vapors are both a health risk and a job hazard.
The fact is, there are 3 million injuries in the workplace each year. And, surprisingly, most of these injuries are a result of human error.
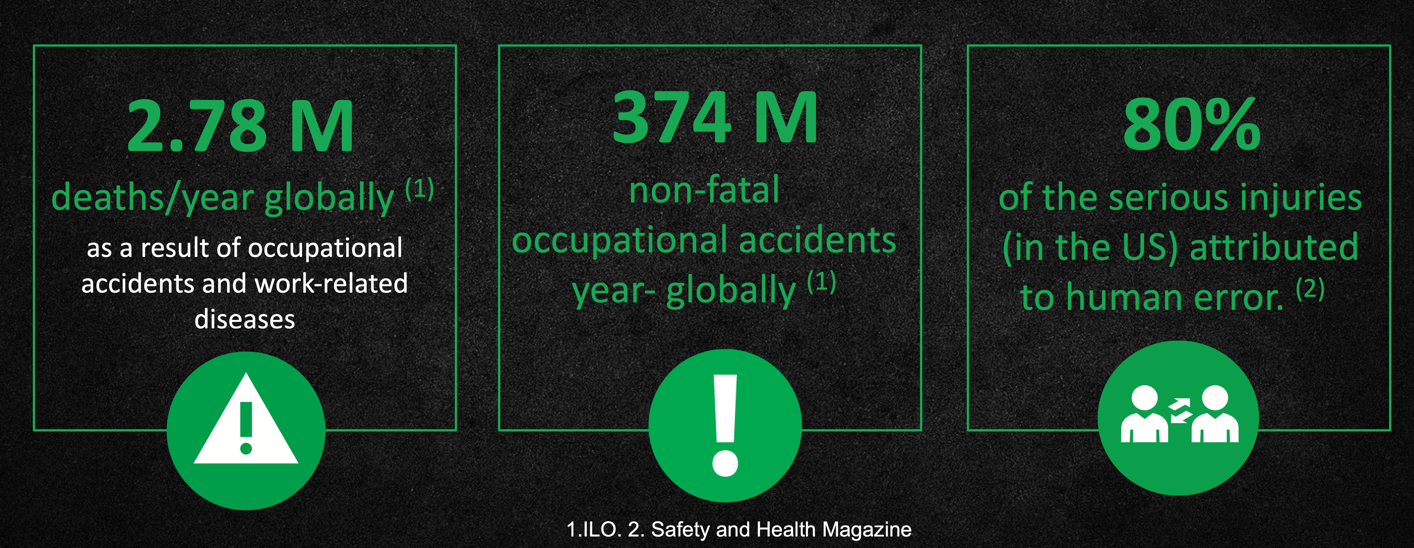
But because one fatality is one too many, something needs to change.
That something?
Leveraging connectivity and new technologies to improve safety compliance, safety monitoring, and personal wellness and productivity.
What is connectivity and why does it matter?
That’s where IIoT connected solutions come into play. Not only does a connected solution help ensure compliance, it also can help create much-needed operational efficiencies.
How?
By solving the problem of having too many disparate FGFD devices. Remember, connectivity is how safety professionals can link their gas detection devices and corresponding data to decision makers – all in support of a more proactive safety culture.
Typically, a proactive safety culture means having the insight and visibility into such safety-related questions as:
- What’s happening?
- Where is it happening?
- Is this a true emergency or a false alarm?
- Do we need to investigate or evacuate?
For those who want to protect high-value personnel and infrastructure assets, a connected FGFD program puts an end to the tension between knowing that something is going on but not knowing exactly what.
So, how do you effectively enable connectivity for FGFD?
Here are some things to consider:
While it’s true that gas detection technologies for oil & gas and chemical process industries have become more sophisticated through the years, thanks to such features as embedded electronics, sophisticated firmware, and spectral techniques, any single device or technology is simply not able to offer the same level of protection that a connected gas and flame detection solution can.
So, start by taking a good, hard look at all aspects of your program. Do you have reliable and durable Fixed Gas & Flame Detection devices? Do these devices have built-in connectivity capabilities? What type of data can the FGFD devices provide? What type of data do you need? Can you easily extract and understand the most critical data? Is your connected solution safe, secure, and easily configured? Do you have a reliable connectivity partner like MSA that shares your safety vision now and for the future?
Use your answers to these questions to guide you to the right solution for your safety program.
Because easy-to-understand data lets you take fast action without distractions, you’ll want to implement a connected solution that’s smart, yet simple. The best solution won’t require a ton of set up or training. Instead, it should provide easy navigation to the information that matters most.
MSA FieldServer FGFD ProtoAir is one such option. This full-featured, cloud-connected gateway is a plug-and-play solution that quickly and easily connects MSA FGFD instruments, as well as other manufacturers’ products. The FieldServer FGFD ProtoAir features a quick, web-based setup that’s built into the gateway. That means you can connect to the cloud for remote connectivity via ethernet, cellular, or wi-fi connection. Plus, ProtoAir is a high-performing, low-cost, visibility-improving gateway that delivers automated alarms, 24/7/365 remote monitoring, and immediate data visualization.
If you’re looking to create a more proactive safety program, it’s smart to leverage a connected solution for FGFD. But because it can take some time to fully incorporate IIoT technologies into the ebb and flow of your safety program and processes, we recommend that you take slow, methodical steps to ease the transition. Keep in mind that connectivity is more than a just a simple platform, it’s a strategy to help your safety program reach its full potential.
Remember, too, that it’s okay to take small steps toward connectivity with the end goal being a solution that:
- Saves time and money monitoring remote locations
- Minimizes downtime due to shutdowns and in-person investigations
- Improves safety by providing full visibility into potentially hazardous situations
- Enhances communication with real-time alarms and notifications
- Provides more accurate insight so that assets remain operational and workers stay safe
If you approach FGFD connectivity in this way, you’ll not only help create and support a more proactive safety culture, but you’ll also effectively eliminate the “Who do we call?” and “What do we do now?” questions from the operational equation.
To learn more about the secret weapon of connectivity, contact us.