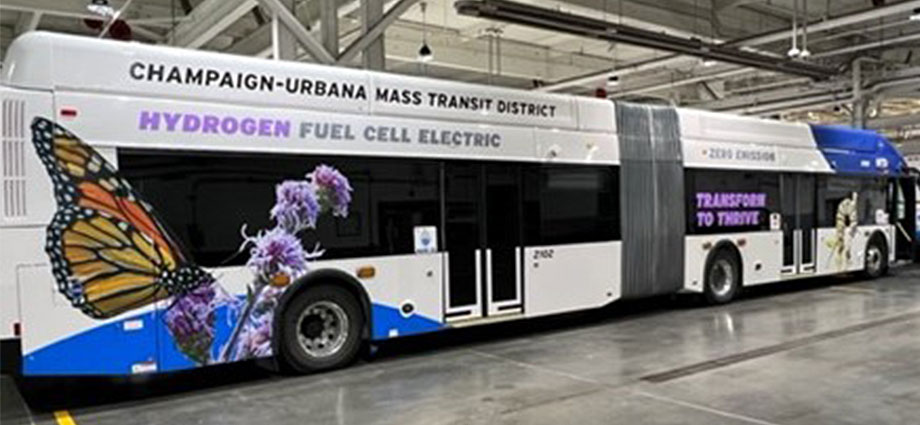
Most of the world has entered the race to drastically cut carbon emissions. The when and how of making it happen varies by organization, of course, but most experts agree that clean, renewable energy sources will be key to creating a carbon negative world.
Which is why in 2018, the Champaign-Urbana Mass Transit District (MTD) became the nation’s first transit agency to commercially order 60-foot articulated hydrogen fuel cell buses. Soon after, MTD began a much-needed update to their infrastructure and technology to accommodate the new fleet, followed by the construction of the hydrogen production plant and new solar array.
Creating sustainable transportation like this is no small feat. Which is why, along with its many benefits comes a host of challenges, including safety-related concerns.
Here’s how we helped this future-forward mass transit organization ensure the safety of their employees and high-value assets within an environment that’s now home to an on-site hydrogen production station.
Challenge: Gas Detection Notifications
“Our zero-emission fleet technology is an advancement in climate resiliency,” says Kirk Kirkland, Facilities Director for MTD, “It literally has put us on the cutting-edge of public transportation powered by clean fuel. To get to this point, however, we had four projects going on all at the same time. In addition to building the buses and bringing them on-site, we had a temporary fueling station, construction of a hydrogen station, and a 2-megawatt solar array field of nearly 5,500 panels in the works. Throughout construction and even now, we needed a reliable system that not only could detect hydrogen, nitrogen dioxide, and carbon monoxide gases, but also immediately notify us if there was a leak or issue.”
First order of business? Install a fixed gas detection system; namely, the SMC Sentry IT from MSA, designed specifically for facilities facing the risk of combustible or toxic gases. Because the system was going to be installed in a bus garage away from the very personnel charged with monitoring the system, MTD also needed a solution that could deliver real-time notifications and alarms.
“Frankly, we were worried about notifications,” says Kirkland. “The bus garage is not the best place to see or hear alarms. A hydrogen system with built-in alarms, horns, and lights that’s like a fire alarm is good, but for nitrogen dioxide and carbon monoxide, we needed something more than just a light on a panel. We were looking for a solution that would allow us to monitor and communicate with the system from another part of the building where most of our offices and personnel are located.”
We needed something more than just a light on a panel. We were looking for a solution that would allow us to remotely monitor and communicate with the system.
Kirk Kirkland, Facilities Director, MTD
But that wasn’t MTD’s only concern. The organization also needed the solution to be compliant with local fire department regulations. That’s because, even though MTD operates on a 24/7 schedule most of the year, during the summer, there’s a gap between midnight and 5 a.m. when nobody is on shift to monitor the system. MTD’s initial idea was to set things up so that a notification from their monitoring system would go to the local fire department. That methodology, however, does not align with local regulations and was, therefore, prohibited.
Solution: Integrated, Real-Time Monitoring and Alarming
What MTD needed was an independent life safety and building automation solution that could provide remote monitoring, control, and alarming.
But because MTD was the first transit agency in the country to adopt a hydrogen fleet fueled entirely from their own 100% renewable source, there was a steep learning curve for just about everything – including safety.
What MTD needed was a safety expert. Enter MSA Safety.
Upon seeing MSA’s presentation, MTD knew they had to choose the SMC Sentry fixed gas detection system, which features advanced sensing algorithms, protocols, web technologies, and cloud connectivity. They also chose to pair the system with the FieldServer ProtoNode.
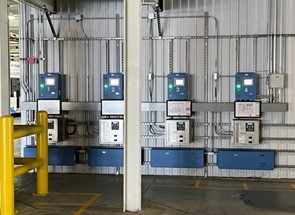
This enabled them to connect the Sentry IT system to the FieldServer Manager, which sends real-time text and email notifications to appropriate personnel, alerting them to the potential presence of hazardous or combustible gasses.
After a series of unfortunate and unavoidable obstacles at MTD (including a global pandemic, personnel changes, relocation of the system through construction of the production plant, and inaccurate sensor and zone mapping), MTD successfully configured the system. Now they are actively monitoring what they want the way they want – that means detecting carbon monoxide at levels lower than required by OSHA, as well as customizing the hydrogen detection at levels below 25% of LEL if needed.
“Obviously, we’re most concerned with hydrogen,” explains Kirkland. “In fact, some of our team members only want to see hydrogen alarms. This system is great because it lets them choose the parameters they want. But we also have to monitor nitrogen dioxide and carbon monoxide. We haven’t had any nitrogen dioxide alarms. As for carbon monoxide, we’ve assigned two utility workers to answer and reset those alarms. Most of the time when carbon monoxide alarms go off, by the time we walk to the panel, it’s already cleared. We’re confident, though, that we’ll have the notifications we need should there be a higher concentration of any gas or should any of the gasses be present for longer periods of time.”
Result: Hydrogen Production Station Safety
The addition of the FieldServer ProtoNode to the Sentry IT gas detection system gives MTD a high-performing, low-cost IIoT gateway that enables both SMS text and email notification for trouble or alarm conditions.
MTD has completed initial configuration and is continuing to fine tune its operation. In fact, the organization plans to configure the system so that they also can send notifications to personnel on the second floor of a building where training offices and vehicle radio personnel are located.
“Things are working very well,” says Kirkland. “We’ve set up the types of events we want to monitor and we’ve configured the high-low settings we want for hydrogen. We’re still tweaking some things like graphics, but we’re absolutely confident that it will do everything we want and need it to do to keep our first-of-its-kind zero emission fleet technology and our staff safe.”