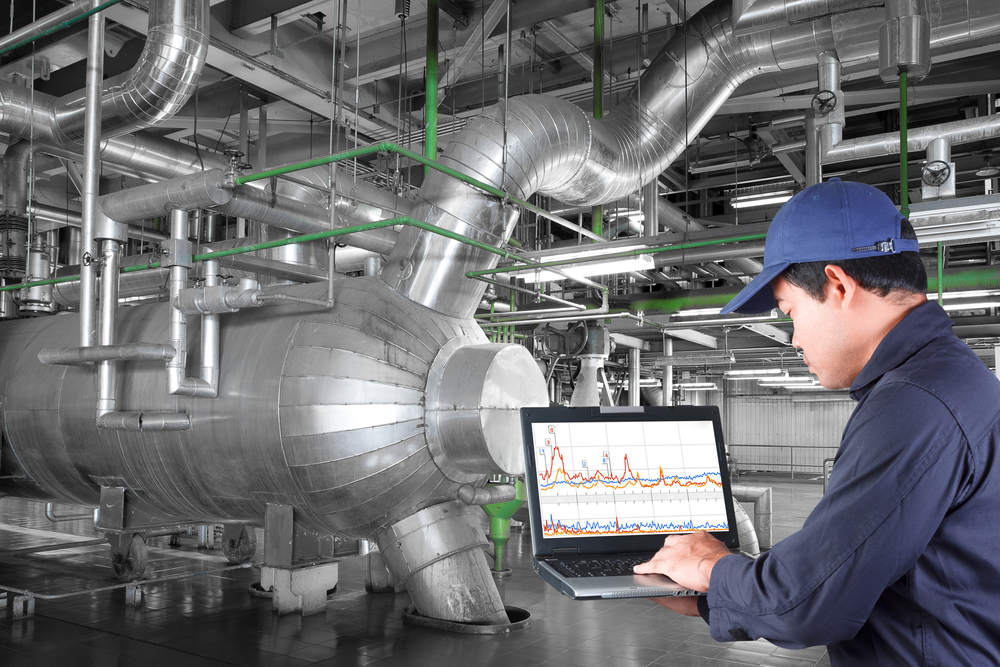
With many nonessential businesses and industries being asked to close by state and local governments, there has been a massive spike in the amount of Americans working from home.
While we’re starting to see a number of states begin to ease away from that guidance and those restrictions and put their citizens back to work, there are many states that could keep these policies in effect for a number of months into the future.This great telework experiment that has been happening across the nation could have lasting impacts on our country and how it works. According to a recent survey of CFOs by the analyst firm, Gartner, approximately 74 percent of the executives polled are looking to have at least 5 percent of their previously on-site staff continue working remotely in the future.
However, these exciting new telework trends simply don’t apply to everyone. There is a large population of Americans that are deemed “essential” by their employers because they need to be on-site, managing and maintaining important commercial and industrial equipment and devices. But that, too, could be changing.
Customer demand for Internet and cloud-enabled IIoT devices with the capability for remote access are forcing many equipment manufacturers to embrace the new technology, which could have far-reaching effects on what it means to be an essential worker.
To learn more about these new technologies and how prevalent they’re becoming in the commercial and industrial equipment industry, we recently sat down with Richard Theron, a Product Manager at cloud gateway solution provider, Sierra Monitor,.
Here is what Richard had to say:
Honestly? None, or very little. For many of the facilities and maintenance people that are responsible for overseeing commercial and industrial equipment and devices, there really is no other choice than to be onsite. They need to be there to identify problems, troubleshoot problems, if possible, and then engage with the equipment manufacturer if additional support is needed.
In fact, there are really two groups of people that have to be onsite. The first are the maintenance teams and facilities teams for the equipment owners. But often, if they need further assistance, they’ll reach out to the equipment manufacturer for help. The manufacturer will then roll a truck to repair that equipment. This means that even more essential employees are onsite. Ultimately, commercial and industrial equipment and devices are necessary to keep business moving. And every company in every industry, essential or otherwise, relies on it. The people that those companies rely on to keep things running are often asked to work onsite, even if much of the remaining workforce is working remotely.
Richard Theron: That functionality is actually available for commercial and industrial devices. At least, it can be. It’s possible. The technology is available, but the adoption of the technology is really just beginning.
The good thing for essential workers is that the adoption of that technology is accelerating. Each month we see a larger ecosystem of commercial and industrial equipment and devices emerging that are able to be accessed remotely and managed remotely via smartphone or other Internet-connected device.
It’s becoming pretty prevalent across a number of industries. And, while not all manufacturers are on board yet, they’re going to be soon, because they have to be.
For the early adopters of remote access, it was a competitive advantage. They were able to tell their customers that their employees could monitor and manage their devices remotely, which was a very intriguing and enticing capability to offer.
Over time, more and more customers started demanding remote access because they knew it was available and it gave their employees more flexibility while also making them more efficient. Now, the equipment manufacturers that were slow to embrace remote access are scrambling to catch up to their competitors and to meet customer demands for the technology.
But that’s really just one part of the equation. The demand signal for remote access is really coming from both the customer and from within the manufacturer, itself. That’s because remote access can benefit the manufacturer, as well. To learn more about the benefits of cloud-enabling commercial and industrial devices, click the image above to download a complimentary copy of, “The HVAC as a Service Revolution.”
By enabling remote access and monitoring of devices, the manufacturer can offer better, more proactive support to their customers. They can roll better-equipped and prepared service trucks. They can even use the device data to improve their equipment sales and to help sell service contracts. It lets them better utilize internal resources, better serve their customers, and generate extra revenue.
It’s not difficult at all,it just requires the addition of a cloud gateway. It’s a simple addition to the product line. In fact, many manufacturers are already implementing gateways into their devices to enable them to connect to building management and building automation systems.
By using a gateway that also enables connectivity to the cloud, they can make their devices connect to building management and the cloud, making it possible to access their devices remotely.
Gateways aren’t just capable of cloud-enabling new devices. An older device that never connected to the Internet could have been remote access enabled via a cloud gateway.
One of the most important capabilities is remote monitoring, watching a device’s status, and being able to access device data remotely. What’s most exciting about that is, once you have the ability to monitor a device remotely, you can enable more predictive maintenance.
For example, let’s say you’re monitoring the power consumption of a device and you see that the device’s power consumption is going up, there is a chance that the motor is wearing down or there is something else going wrong. If we can see how much energy that motor is drawing, we could see that something is wrong and get someone out there to fix it before it breaks.
That level of predictive maintenance is important for a number of reasons. Think about a boiler in a hospital. Hospitals can’t function without hot water. If we can see the device data and see that the water pressure and temperature is dropping, it tells us that there is a problem. We can then look at the data to make a diagnosis, determine what is wrong, and get it fixed before it breaks, leaving the hospital without hot water.
That’s only possible if we see those red flags. And we can see those red flags anywhere and at any time if we can monitor devices remotely.
Another capability is remote management. Imagine being able to push a firmware update to a device, or to every similar device, all at once and from a remote location. With a cloud-enabled device, as long as you have Internet access, you can push those firmware updates to those devices from anywhere without ever having to engage with the device.
We’ve seen something similar and very exciting in the lighting industry, where some manufacturers are remotely configuring new devices as soon as they’re plugged in and connected to the Internet. This means that the person doing the installation doesn’t need to know anything about the device or how to configure it, it’s all done by the experts that know the device the best,the company that manufactured it.
All of these remote capabilities are possible. But only if the devices are cloud-enabled.
In part two of our two-part conversation with Richard, we’ll look at how enabling remote access also creates security vulnerabilities for devices, and what manufacturers can do to mitigate the problem.
To learn more about the benefits of cloud-enabling commercial and industrial equipment, click HERE to download a complimentary copy of the, “HVAC as a Service Revolution,” eBook.